Every Engine Must Exhale
15th July 2024
A proper exhaust system and its maintenance is vital to an engine’s performance. “Out goes the bad air, in comes the good”. A properly sized and well-designed marine exhaust system is the best way to get rid of the bad air and optimize an engine’s performance.
Anything that inhibits the flow of exhaust gases creates excessive back pressure, which decreases the amount of horsepower delivered. Back pressure is created by the length of the exhaust tube, its diameter, the bends along the way, plus the restrictions imposed by silencers, couplings, valves, and water injectors. Short fat and straight is better than long, skinny and winding.
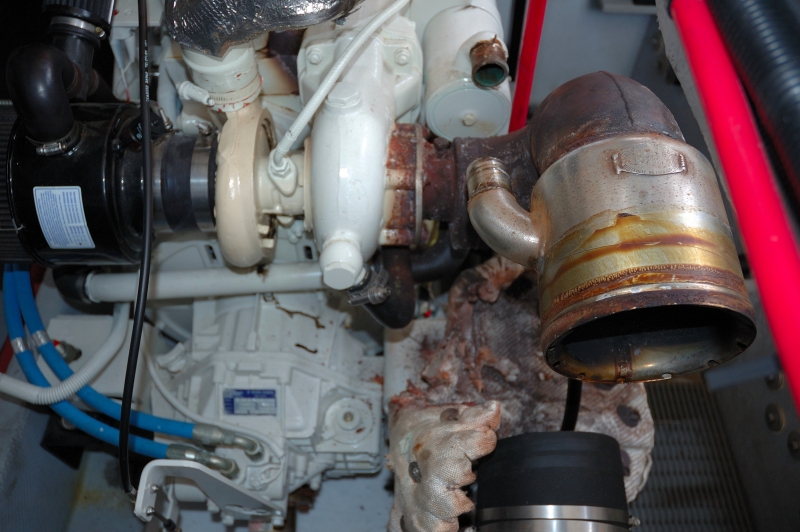
Marine exhaust systems for inboard engines are divided into two basic types, dry and wet. Most yachts have wet exhausts, generally injecting water from the engine’s raw-water discharge into the exhaust stream, downstream of the exhaust manifold or turbocharger, to cool the gases and quiet engine noise. The cooled gases also allow the use of fiberglass, rubber, and silicone components. Such systems are also able to safely discharge the cooled exhaust through the hull near or below the waterline.
Dry exhaust systems have been around the longest, but they’re primarily used on commercial vessels or other specialty applications, like high performance craft. Dry exhausts require all-steel/iron construction to withstand the higher temperatures. The discharge must be topside, clear of guest areas, but in unfavorable wind conditions, such a location may deposit soot on both the deck and guests.
Wet systems commonly use a perforated ring – it may be a separate component, an integral part of the riser when there is a need to get a downward slope on the exhaust line or part of the silencer – to inject cooling water into the exhaust. Boat owners have many stock silencers to choose from, or they can contract with a specialty fabricator for custom units in fiberglass, stainless steel, or aluminum. They’re available in both vertical and axial configurations, to suit the space available in any engine room.
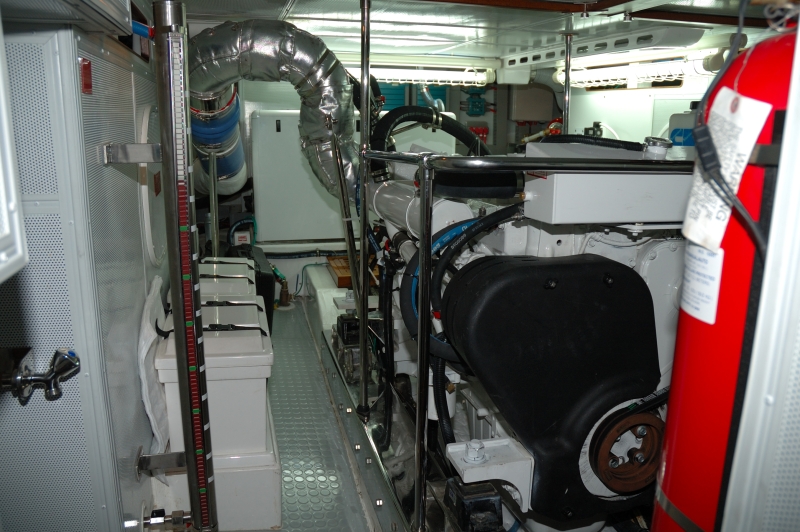
In addition to incorporating the water injector, risers protect against water flooding back into the engine. Yachts that routinely back down, such as sport-fishermen vessels, and have exhaust outlets in the transom will benefit from having surge tubes at the forward end of the line to prevent back-flooding.
To circumvent the back-flooding noise, soot and fumes of transom exhausts, many yachts have underwater exhausts. A bypass must be fitted above the waterline to prevent excessive back pressure at idle, and a solenoid-operated valve is sometimes included to close the bypass once the yacht is under way.
If the underwater exhaust is not of continuous, substantial construction to well above the waterline, it should include a shut-off valve. The outlets of such exhausts shouldn’t lead the gases into the props, rudders, trim tabs, or bottom strakes, because the aeration and turbulence undermine the efficiency of the props and the hydrodynamic effectiveness of the appendages. All components of the system should be suitable for marine-exhaust temperatures and chemical exposure. Look for ABYC, NMMA and/or SAE approval stamps on hoses and flex bellows, and keep in mind that type 316 stainless steel is preferred to the more commonly found types 302 or 304 for hose clamps.
Every section of the system should be insulated where appropriate, to protect crew members and to keep heat from escaping into the engine room. All components should be well supported by resilient mounts or hangers. Sections upstream of the flex bellows should be supported by the engine, to move with it, and sections downstream should be supported from the yacht’s structure, independent of the engine’s movement.
If you just monitor an engine temperature gauge, your exhaust system may be damaged long before you notice overheating. And never ignore overheating. “It must be a problem with the gauge’ isn’t the correct response.
Exhaust systems. like all boat systems, need regular inspection to ensure they continue to function properly. Check hoses for leaks, kinks, chafing, bulging and other signs of deterioration. Verify each hose is doubled clamped and that hose clamps are tight and free off corrosion. Also look for leaks at other system components, paying special attention to engine exhaust manifolds and elbow joints. Manifolds and risers should be periodically removed, cleaned and pressure tested. Heat-resistant exhaust insulation covering should also be removed periodically to allow a full inspection.